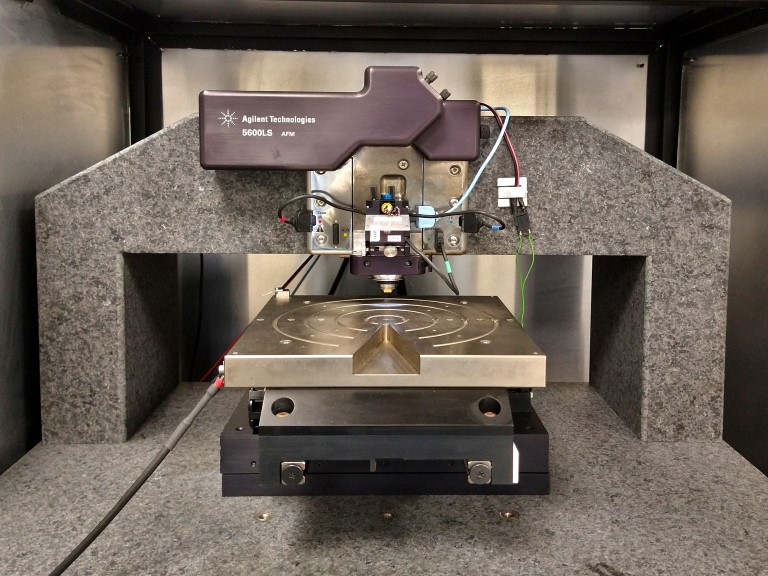
AFM System – Keysight 5600LS
Details
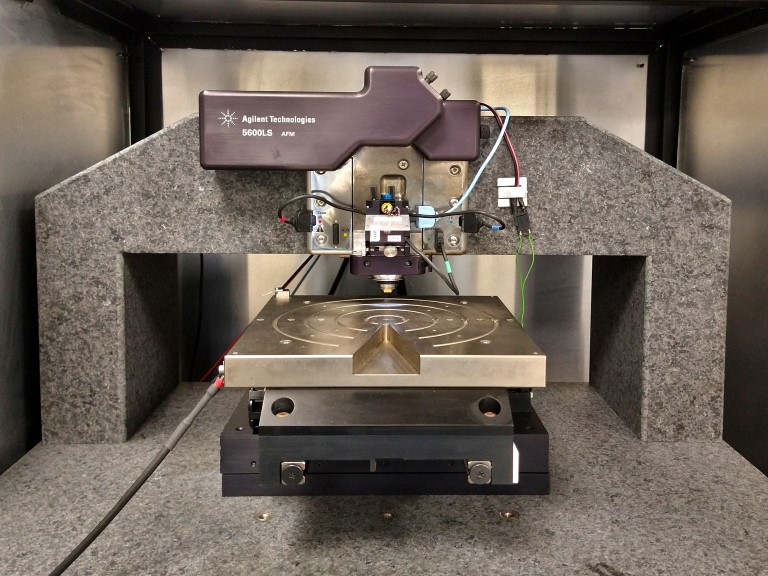
Description
The modular 5600LS AFM system allows imaging of both large samples (in air) and small samples (in air, or in liquid under temperature control).
The 5600LS utilizes a 200 mm x 200 mm, fully addressable and programmable stage, as well as a low-noise AFM design.
Samples up to 8” in diameter and 30mm tall are easily accepted by the 200mm vacuum chuck.
The stage accommodates a 300 mm wafer with repositioning.
Working principle
Atomic force microscopy (AFM) is a high-resolution scanning probe microscopy technique, with demonstrated resolution below the nanometer.
The AFM consists of a cantilever with a sharp tip (probe) at its end that is used to scan the specimen surface. The cantilever is typically made of silicon or silicon nitride, with a tip radius of curvature on the order of nanometers.
When the tip is brought into proximity of a sample surface (few nanometers), forces between the tip and the sample lead to a deflection of the cantilever. These deflections are measured using a laser beam, which reflects on the cantilever and is collected by a four sectors photodetector. In most cases, a feedback mechanism is employed to adjust the tip-to-sample distance to maintain a constant force between the tip and the sample. The tip is mounted on a piezoelectric system responsible for scanning in the x, y and z directions.
The AFM is usually operated in two modes: static mode and dynamic (AC or “tapping”) mode. In static mode, the cantilever is kept in close contact with the sample surface during the scan. In the dynamic mode, the cantilever is externally oscillated close to its fundamental resonance frequency.
Specifications
System: The 5600LS combines stable, low-noise AFM imaging with high-speed, very flat, easily reproducible displacement over the stage travel range. The automated tip approach feature of the AFM minimizes damage to delicate sample structures. Motorized optical zoom and focus capabilities facilitate the automatic pre-approach, simplifying setting the initial tip-sample separation. The 5600LS also allows users to perform simple, software-driven, point-and-shoot AFM imaging of an area of interest based on an optical view.
Stage: The 5600LS system’s programmable, motorized stage enables fast, accurate probe positioning for imaging and mapping both large and small specimens alike. Investigators can precisely locate and identify an area of interest and, with the coordinates stored, automatically reposition the sample quickly and accurately for further study. Multiple locations can be programmed into the system.
Scanner: The 5600LS system is equipped with a 90 µm x 90 µm top-down scanner which utilize interchangeable nose cones that enable users to switch imaging modes quickly and conveniently.
MAC Mode III Controller: The Keysight MAC Mode III Controller provides 3 user-configurable lock-in amplifiers, affording large application flexibility. Additionally, it has internal expansion capability to allow the future addition of advanced imaging and analytical modes. Optimized for single-pass KFM/EFM concurrent imaging, it enables the collection of simultaneous topography and surface potential data using a servo-on-height cantilever approach that is insensitive to scanner drift. In addition to KFM/EFM and piezo force microscopy, MAC Mode III allows the use of higher resonance modes of the cantilever. Higher harmonic imaging provides contrast different from that seen with fundamental amplitude and phase signals. This technique can be utilized to collect additional information about mechanical properties of the sample surface.
Imaging Modes: The 5600LS is compatible with contact mode, acoustic AC mode, phase imaging, STM, LFM, KFM/EFM, MFM, force modulation, current sensing, and MAC Mode, a nondestructive technique for imaging delicate samples in air or liquid.
